Battery Recycling
Given that battery manufacturing is resource intensive, battery recycling has gained attention as a means to reduce greenhouse gas emissions in the mining, sourcing and producing materials, prevent resource depletion and thereby reduce environmental impacts. As a leading battery manufacturer, LG Energy Solution strives to maximize the environmental, social and economic values of battery recycling and to contribute to building circular battery ecosystem.
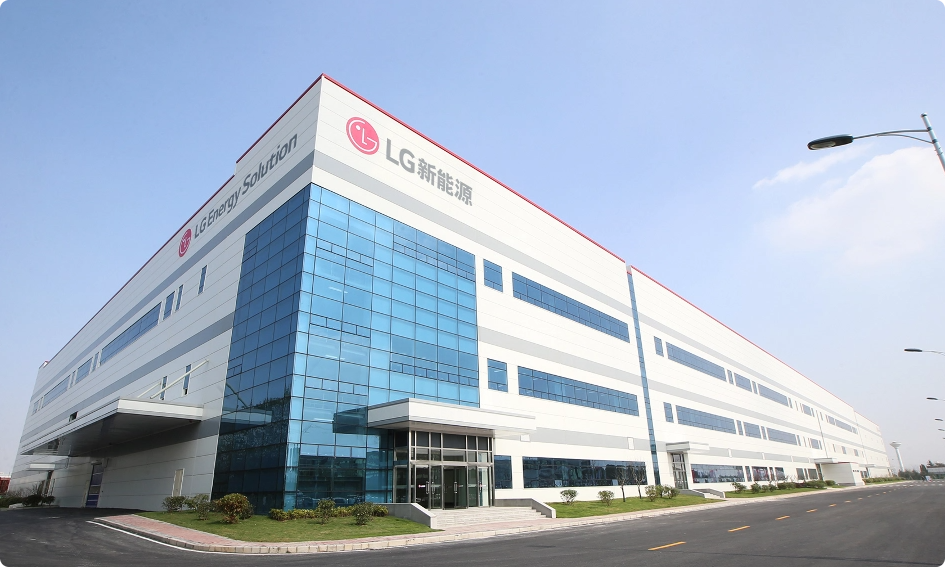
Nanjing Plant, China – Closed Loop Established in 2022
To that end, LG Energy Solution is building a closed loop system where non-reusable batteries and scraps generated during production are collected and recycled; and the extracted materials are reinjected into the production stage. Based on strategic cooperation with leading recycling companies, we are establishing a system to collect end-of-life batteries at each global manufacturing site. In 2022, we established the closed loop at Nanjing Plant in China. We plan to have it available in all global sites, including Korea, Europe, and the United States, by 2025.
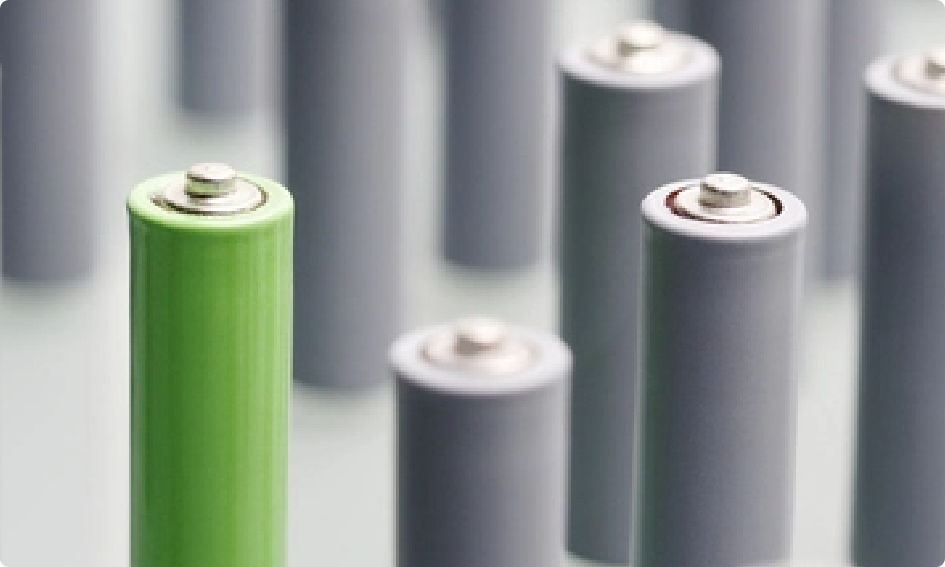
We also operate a *DPMS and a waste NMP recovery facility to manage battery waste thoroughly and are constantly working to increase the recycling rate by developing treatment technologies for effluents from anode materials.
* DPMS (Disposal Product Management System ) : A system that manages the information and history of the entire process from waste registration, storage, transport, and proper treatment for thorough tracking and management of waste
Battery Reuse
End-of-life batteries not fit for automotive use are collected through a regional collection system and assessed for determination of its second life application. Reusable batteries are transported and stored separately.
-
· Reconditioning
Reusable batteries are classified based on their conditions – through physical and chemical analysis and residual capacity prediction – and second life applications
-
· Refurbishing
Reusable batteries are tailored to meet the technical requirements and safety standards of different applications Cost competitiveness is ensured by optimal designs that prioritize safety, and efficiency of manufacturing procedures.
Batteries ready for reuse are distributed to the markets that can ensure their optimal use; and a collection system for recycling is designed.
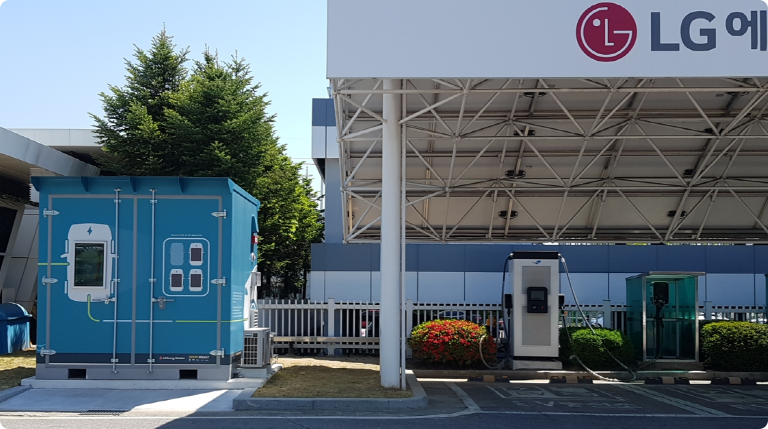
Ochang Energy Plant, Korea
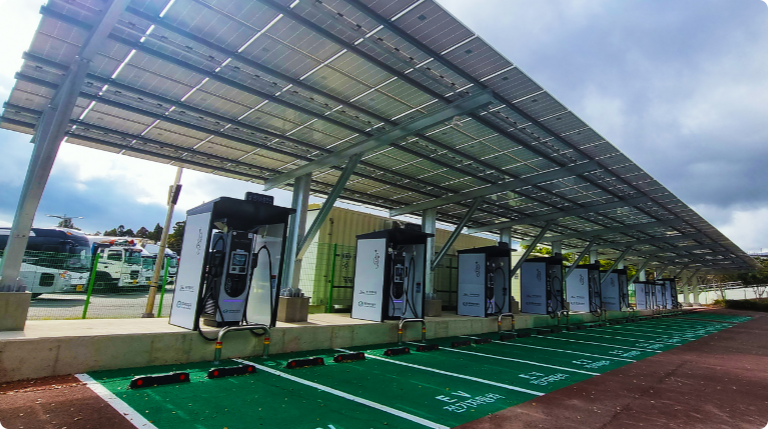
Jeju Wolrd Cup Stadium, Korea