Quality Management System
With a view to ensuring high quality and reliability standards for all products and processes, LG Energy Solution has put in place a quality management system across all facilities certified with IATF 16949:2016 Automotive Quality Management System and ISO 9001:2015 Quality Management System standards. We intend to maintain the effective operations of such a quality management system through a continued process of 1) developing and implementing quality management programs, 2) evaluating, at least annually, the progress against targets, and 3) enhancing internal standards and processes based on the findings from the regular evaluation and stakeholder feedback.
Status of Certifications Acquired
At LG Energy Solution, the headquarters, manufacturing plants in operation and R&D centers are certified with IATF 16949:2016 Automotive Quality Management System and ISO 9001:2015 Quality Management System standards. As part of certification process, we conduct third-party audits of quality management system, including surveillance or maintenance audits and re-certification audits. Further, we conduct internal audits, annually, to ensure facility-level compliance with company-wide regulations and standards and continuous improvement, thereby exceeding stakeholder expectations.
LG Energy Solution has obtained the international certificate of quality system for 100% of its wholly-owned manufacturing plants in operation (as of March 2025).
Category | Name | Certifications Acquired |
---|---|---|
Korea | Headquarters | IATF 16949 ISO 9001 |
R&D Campus Daejeon | IATF 16949 ISO 9001 |
|
R&D Campus Gwacheon | IATF 16949 ISO 9001 |
|
Ochang Energy Plant | IATF 16949 ISO 9001 |
|
Ochang Energy Plant2 | IATF 16949 ISO 9001 |
|
China | LG Energy Solution (Nanjing) Co., Ltd. | IATF 16949 ISO 9001 |
LG Energy Solution Battery (Nanjing) Co., Ltd. | IATF 16949 | |
LG Energy Solution Technology (Nanjing) Co., Ltd. | IATF 16949 | |
Poland | LG Energy Solution Wroclaw sp. z o.o. | IATF 16949 ISO 9001 |
USA | LG Energy Solution Michigan, Inc. | IATF 16949 ISO 9001 |
Canada | Nextstar Energy Inc. (Stellantis Joint Venture) | IATF 16949 LOC* |
For the production facilities under construction, we plan to obtain the certificate, carefully considering the start of production and the conditions required to certification acquisition. For example, IATF 16949 requires a production track record and operational performance for at least one year.
*To qualify for IATF 16949 certification, organizations must demonstrate a minimum of one year of production and operational performance, or obtain a Letter of Conformity (LOC) from the certification body if their operational history is less than one year.
Quality Management Framework
Quality Risk Prevention and Management Process
LG Energy Solution established a company-wide, comprehensive quality assurance framework to ensure rigorous quality management. Our internal quality standards are designed to not only meet but exceed international standards. Such stringent standards serve as the foundation for systematic verification of product quality at each stage of entire value chain, encompassing procurement, development, production, and distribution. Furthermore, exhaustive quality and safety testing, including precautionary testing for emerging quality and safety concerns, is conducted across all products, while various supply stability management strategies are in place to proactively identify, prevent and mitigate any potential risk within our supply chains.
Customer-Oriented
Quality Management Process
Procurement
Securing a stable supply of parts and materials is one of key elements of product safety and quality management. LG Energy Solution puts in place various strategies to mitigate risk associated with disruption in parts and materials sourcing. Potential emergency cases are categorized by factor that causes supply chain disruption, including natural disaster, workplace accident, suppliers’ management issue such as bankruptcy, layoff or strikes, geopolitical events and related price fluctuation. For each category of emergency case, a formalized process and manual is put in place that encompasses case classification, reporting protocol, operation of emergency taskforce, and mitigation and remediation planning. Mitigation measures are planned in a phased manner – in the short-term, mitigation measures include temporary sourcing of alternative, production plan adjustment; in the mid- to long-term, mitigation measures vary ranging from dual sourcing, alternative/new supplier identification, to the change of manufacturing site. The category-specific processes and manuals are reviewed and updated on a regular basis to ensure effectiveness of product safety and quality management process and to minimize any adverse impact and prevent recurrence of such event.
Development
At the product development stage, LG Energy Solution follows a rigorous ‘Product Quality Planning Process’ to ensure the design of products meets customers' quality requirements and international standards. With in-house capacity to test product performance, safety, reliability from the design to materials & parts approval phases, we identify and mitigate potential or emerging quality and safety concerns in a preemptive manner. Each of newly developed products, before mass production, should undergo relevant international certification process.
Comprehensive Product Quality and Safety Assurance
LG Energy Solution is committed to ensuring that its products meet the highest standards of quality and safety throughout their lifecycle. This is demonstrated through rigorous product reliability, environmental, and safety testing during the development phase, followed by regular inspections during mass production phase. Reliability testing ensures product performance consistency during its intended usage period. Environmental testing evaluates a product’s ability to function in conditions like extreme temperatures, humidity, vibration, and shock. Safety testing is performed to verify the product's resilience in abnormal situations that may arise during its usage period. It simulates scenarios, including collision, drop, short circuit, overcharge and over-discharge.Through these comprehensive testing protocols, LG Energy Solution guarantees that its products are safe, reliable, and of the highest quality for end customers.
Production
At LG Energy Solution, we maintain strict quality control measures throughout the production process, conducting thorough inspections of all parts and products at each step. We have put in place various risk mitigation process such as dual sourcing, to mitigate potential risks caused by unexpected changes in the project volume and/or in supply chains.
Further, to mitigate potential risk caused by unexpected issue or disruption in the production line, we secure backup manufacturing sites. This helps to maintain operational reliability and business continuity.
Delivery
At LG Energy Solution, outgoing quality controls are conducted in accordance with quality assurance protocols tailored to the respective customer requirements. We adhere to stringent transportation and storage standards, carefully considering product specifications and logistical conditions to ensure optimal quality. The packaging design takes into account factors that may affect product safety and quality, such as temperature and humidity variations and potential external impacts during delivery. In addition, a varied range of robust supply chain stability management strategies are in place to mitigate potential risks such as a sudden surge in customer demand and raw material supply imbalances. These include dual sourcing, securing external warehousing, utilizing Vendor Managed Inventory (VMI), and optimizing safety stock.
Quality Risk Response Process
Quality issues can arise at any stage of business, including product development, components or parts sourcing, inventory storage, and product delivery. Therefore, it is crucial to establish a company-wide system and process that enables to promptly identify, respond to and efficiently mitigate any quality risk. LG Energy Solution’s approach to quality risk response is:
- Operate a company-wide risk management system to proactively identify, prevent, mitigate and effectively respond to potential and/or actual risks in various aspects of business
- Apply different processes and protocols including crisis management, business continuity management, and risk management, depending on the type and root cause of risk.
Business Continuity Management System (BCMS)
LG Energy Solution is dedicated to maintaining the quality of all products and services and ensuring timely delivery to customers during and after disruptions. Our Business Continuity Management System (BCMS) is established based on and certified with ISO 22301 to validate and enhance the continuity, consistency, and effectiveness of our risk management system. Further, all of our operating sites undergo internal evaluation based on our own risk management criteria, which align with ISO 22301 standards.
Capacity Building in Quality Management
Through LG Energy Solution Battery Academy (LBA), we offer a comprehensive training and capacity development program designed to enhance employee skills and capabilities in assuming respective role. The program is offered to all employees regardless of their position or employment contract type.
In particular, the quality managers across all our facilities worldwide are regularly provided with specialized training in various areas, including quality management, product safety, reliability & statistics, and relevant global regulations. The training courses are complemented with on-site hands-on training and education to further enhance their understanding and capability in quality management.
Further, to promote awareness and foster a culture of quality assurance in each member’s daily work, all employees are offered with Compliance Training Programs, including a ‘Quality Assurance for Customer Satisfaction and Quality Mindset’ course which is mandatory for all employees and is conducted twice a year.
Supplier Quality Management
LG Energy Solution’s quality management integrates a systematic supplier quality management, which aims to ensure consistency and stability in quality and continuous improvement of suppliers’ capability in quality assurance and control. Through a ‘Supplier Quality Management System,’ we monitor real-time data on various indicators of suppliers quality and carry out product reliability risk management.
Supplier Quality Assurance System
LG Energy Solution operates a comprehensive ‘Supplier Quality Assurance System’ that regularly assesses the quality management level of all our suppliers. Key assessment criteria includes customer requirements and global standards, and the scope of assessment is suppliers' quality management systems and processes. The assessment framework is regularly reviewed and updated to ensure that our products meet the expectations from our global customers. In addition to the regular assessments, we conduct ad-hoc evaluations of our suppliers' quality assurance capacity and quality improvement programs. This approach enables us to continuously strengthen our 'Supplier Quality Assurance System’ and ensure that our products consistently meet the highest standards of quality and reliability.
Supplier Quality Certification Process and Capacity Building Program
In order to achieve the highest level of product quality and safety, it is crucial to assess and manage suppliers' product quality and enhance their quality management capacity. LG Energy Solution runs a supplier quality assessment program on a quarterly basis, the results of which are tied with certification, incentive/penalty programs and capacity building initiatives. The assessment program is designed to evaluate each supplier’s quality management system, quality performance and preventive quality control, and rank them in five levels – S, A, B, C and D – based on the score (Q-Score). LG Energy Solution issues certificates and the record of certification is archived and tracked through our Supplier Quality Management System (QMS).
Those suppliers designated with two lowest ranks are required to participate in the "Supplier Quality Rank & Rank Up Program," designed to address their weaknesses and areas for improvement. LG Energy Solution also utilizes this ranking system for the "Supplier New Biz. Hold (SNBH)" program. Under this program, suppliers who receive the lowest D for two consecutive years are excluded from our vendor pool and restricted from entering into new business contracts with LG Energy Solution. This measure ensures that we maintain a high standard of quality and performance from our suppliers, and encourages suppliers’ continuous improvement and adherence to our quality management requirements.
Rank Up Programs
Quality System/Process Improvement
Manufacturing Process Management System Improvement
Lean Six Sigma based Chronic Defect Improvement
Digital
transformation
Supplier Capacity Building Initiatives
SQM Academy
LG Energy Solution provides a quality management training program, called SQM Academy, annually for all of our suppliers. Our program offers a range of courses designed to equip our partners with the necessary skills and knowledge to secure global competitiveness in quality.
Examples of Courses
SPC(Statistical Process Control), PFMEA(Process Failure Mode & Effects Analysis), Firewall, Initial Stabilization, 4M Process, Run@Rate Audit, Audit(SSQ), PPAP(Production Parts Approval Process), 8D Report, SQ Rank
Supplier Quality Conference
LG Energy Solution strengthens its collaborative relationship with suppliers by hosting a ‘Supplier Quality Conference.’ Through this conference, we exchange information on the current state of materials & parts quality, quality management policies, and introduce best cases of improvement programs. The information and discussions held in the conference provide a solid basis for the design and improvement of our supplier capacity building initiatives.
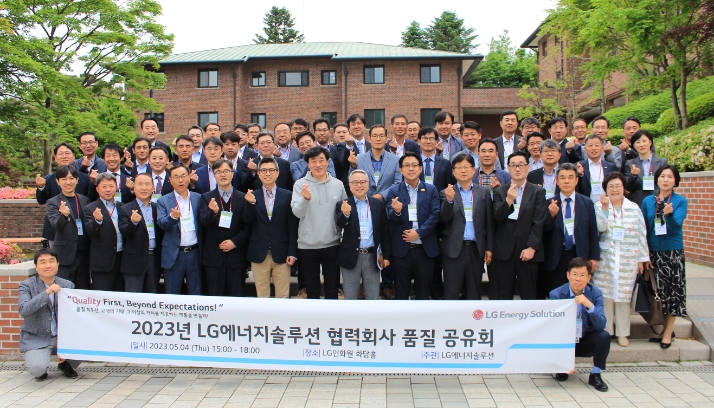
Sub-supplier Qualification Program
LG Energy Solution operates a Sub-supplier Qualification (SSQ) Program aimed at supporting the quality improvement of upstream suppliers by enhancing supplier quality management capacity of Tier-1 suppliers. The SSQ program fosters quality auditors from Tier-1 suppliers and grants them qualifications to evaluate and improve the quality management systems of their suppliers, who are sub-suppliers of LG Energy Solution. Through this system, we strive to secure quality from upstream suppliers in collaboration with our Tier-1 suppliers.